'LINE QC SPECIALIST' Implementation Case Study | Automating quality improvement in manufacturing processes, eliminating defects and visualizing causes
13 Sep 2023
LINE QC SPECIALIST (hereinafter referred to as "LQS") is a quality control system developed by Nano Seimitsu to prevent defective products from being created in the manufacturing process. In this article, we will introduce a case study of TOHOKU MANUFACTURING (Thailand) CO., LTD (hereinafter referred to as "TMT"), which installed this system to improve quality and to make paperless of monitoring sheet..Handwritten-sheets are difficult to determine the cause of the problem.
It is not easy to manage and maintain quality in the manufacturing process to prevent the production of defective products. Management with analog handwritten forms takes time and effort to determine the cause of defects. Many companies are probably struggling with these issues. TMT, an automotive parts processing and manufacturing company in Thailand, was one of them that faced the same problem.
<Issues faced by TMT>
・Wanted to reduce the manufacturing records in paper form
・Handwritten records that rely on human labor have inconsistencies in reliability.
Currently, the company has 50 NC lathes for precision parts machining. Four LQSs are responsible for process quality control of approximately 60% of these machines. Specifically, the LQSs are used to collect data during sampling inspections of parts machining, and as a tool for trend management and quality analysis at the site.
.jpg)
Automates quality data measurement and monitoring and accelerates PDCA cycle
Improve quality and eliminate in-process defects
LQS was developed based on the concept of stopping the outflow of defective products at one-in-a-million (zero PPM) = "eliminating in-process defects" without automatic sorting of all products. The creation of this solution was only possible by a view point of Nano Seimitsu, which itself is also a mass-production manufacturer.
■ Automate manufacturing site monitoring
Automatically monitor three items that cannot be covered by visual inspection alone: "abnormalities of measuring instruments", "central standards and mass production standards", and "measurement locations and measurement frequencies after mass production".
■ Automatic input by digital measuring instrument and quality data judgment in real time
Real-time defect judgment enables immediate response to defects when they occur
■ Big data analysis of measurement data
Automatic database of measurement data enables quick and easy investigation of causes of defective products (operators, machines, tools, etc.) ⇒ Visualization of causes
Especially in the case of cutting machinings such as TMT, changes in quality due to tool wear and other factors can easily increase the defect rate, so daily trend management (monitoring) of machining quality is important. The key to building a manufacturing process that makes it difficult to create defects is to recognize defects as soon as possible, make improvements, and quickly implement the PDCA cycle. LQS is the best solution to achieve this.
Effective for paperless manufacturing and improved production efficiency
Ideal for factories that mass-production machining single parts
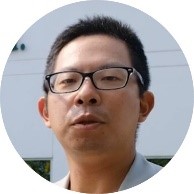
"For many years, we have been having problems managing manufacturing records in paper ledgers. Since introducing LQS, we have not only gone paperless, but also improved our production efficiency considerably by being able to immediately analyze and utilize the measurement data. We manufacture products with tight tolerances (tolerance range 10-70um), and since the implementation, we can check the results on a chart while measuring trends, making it easier to identify trends and variations in dimensions. We currently have four LQSs in place, but we plan to install three more this year to control the process of all of our NC lathes with LQS," said TMT factory manager Mr. Watanabe.
In terms of gradual improvement of process capacity through fixed-point observation of manufacturing records, it is expected to be particularly effective in continuous machining processes such as sites that mass-production machining single parts. This is a revolutionary solution that not only improves quality, but also leads to a highly productive factory where production is always optimized.
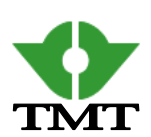
TOHOKU MANUFACTURING(Thailand)CO.,LTD
Established in 2011, the company manufactures precision automotive parts by cold forging and cutting. It has a factory in Pinthong Industrial Park 1. The company's strength lies in its ability to perform integrated processing from forging to cutting
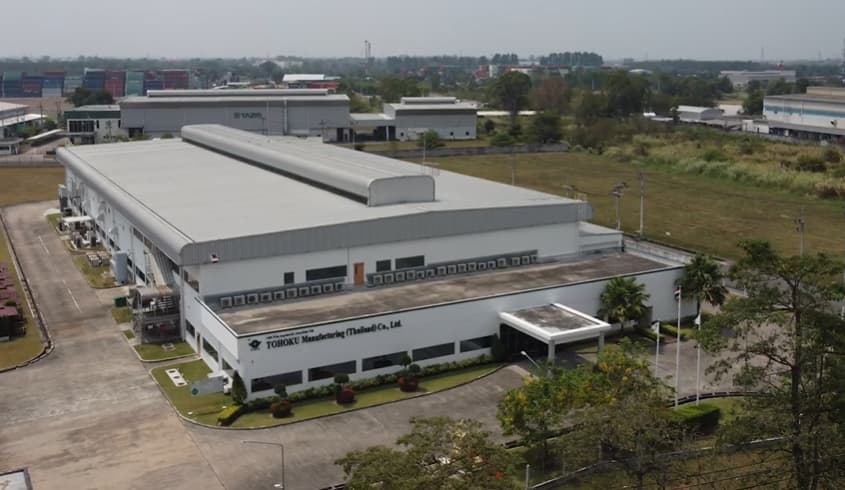